
양봉 적용을 위한 친환경 플라스틱 소초의 제조연구
Abstract
Regenerable and durable plastic honeycomb foundations were produced from polypropylene compounds. The polypropylene compounding compositions were formulated for manufacturing a plastic honeycomb foundation. The polypropylene resin was mixed with the bee-friendly additive materials, such as beeswax, talc, woodflour and compatibilizer. The compounding materials were pelletized through kneading in extruder. The injection mold for the compounds was provided to have a double hexagonal pierced structure considering the durability and nestability of the honeycomb foundation. The mechanical properties of different compositions of polypropylene composites were measured using UTM, in which the beeswax ingredient significantly reduced the strength and hardness. The plastic comb foundations were field-tested at some apiaries. The nesting ability of bees was compared with color types and compounding compositions of the comb foundation. It was improved with beeswax composition, while showing no significant differences in appearance color.
Keywords:
Comb foundation, Polypropylene, Beeswax, Compounding composition, Nesting ability, Field test서 론
꿀벌의 개체수는 자연환경뿐만 아니라 인류의 생활환경에도 매우 밀접한 관계를 가지고 있다. 따라서 최근 산업오염물질의 저감을 통한 양질의 꿀을 생산하기 위한 방안 마련에 관심이 집중되고 있다. 지구환경의 변화로부터 중금속 오염이 없는 친환경 꿀을 안정적으로 생산하기 위해서는 풍부한 밀원의 조성은 물론 친환경적이고 내구성이 좋은 양봉 자재의 개발 또한 매우 중요하다.
현재 사용되고 있는 양봉자재의 핵심인 벌집을 조소할 수 있는 기자재인 소초는 벌의 분비물인 밀랍 (beeswax)을 주로 이용하고 있으며, 이의 원가절감을 위하여 합성 parafÀn wax와 beeswax를 일정 비율로 혼합하여 성형한 파라핀 소초가 많이 사용되고 있다 (Semkiw and Skubida, 2013; Svečnjak et al., 2019). Beeswax 및 parafÀn 소초는 제조가 간편하고 꿀벌과 친화력이 있어 단시간 내에 조소율이 높은 장점을 지니고 있다. 그러나 이들은 저분자의 wax 형태로 기계적 물성이 취약하여 채밀 시의 파손 우려는 물론 내구성이 약하므로 반복사용도 어려우며, 또한 사용 후 폐기물 처리가 번거롭고 꿀벌에 병충해 발생이 심각하여 이를 대체할 새로운 소재로 구성된 소초의 개발이 시급한 실정이다.
미국, 독일 등의 양봉 자재 선진국에서는 polypropylene (PP)의 열가소성 고분자재료를 이용하여 beeswax 소초와 유사한 무늬를 압출시킨 플라스틱 소초 (광)를 제조하고 있다. 플라스틱 벌집 자재는 물 세척이 가능하며, 반영구적으로 사용할 수 있는 이점이 있다. 그러나 이들 소초는 닫힌 형태로서 온도 전달이 느려 beeswax 소초에 비하여 조소율이 낮고 조소시간이 길다. 국내에서도 비록 조소율은 낮으나 PP에 비해 내충격성과 투명성이 높은 polycarbonate (PC) 수지를 원료로 벌집 형태의 육각형이 서로 교차된 준개방형 플라스틱 소초가 개발된 바 있다 (Hwang, 2021). 이들 플라스틱 소초의 특징으로는 내구성이 좋아 반복사용이 가능하고 채밀성이 우수하지만, 조소율 상승을 위해 표면에 beeswax로 코팅처리하고 있으며 가격이 비싼 단점이 있다. 현재 일부 사용되고 있는 플라스틱 소초광으로는 우리나라와 같이 밀원이 부족하고 개화기가 짧은 나라에서 사용하는 데에 한계가 있으므로 (Zhang et al., 2011), 벌들의 특성을 고려한 플라스틱 소초용으로 친환경성의 소재 개발이 필요하다. 최근 이들의 단점을 개선하기 위하여 플라스틱 범용 수지에 꿀벌 친화형 첨가제를 첨가하고 구조를 변경하여, 내구성이 우수하고 조소율이 높은 꿀벌 친화형 플라스틱 소초의 개발에 대한 연구와 상용화가 추진되고 있다.
PP 수지는 저렴하고 재활용도가 높아 친환경적일 뿐만 아니라, 우수한 상용성을 가진 비극성 결정질 중합체로 비독성, 화학적 안정성 및 성형 가공성이 특징적이고 강도 및 내열성이 좋으므로 플라스틱 소초로서 매우 적합한 소재이다. 본 연구에서 beeswax 소초에 비해 가격경쟁력이 있고 내구성이 우수하여 안전하게 채밀이 가능할 뿐만 아니라, beeswax 소초와 거의 동일한 수준의 조소율을 유지할 수 있는 새로운 형태의 꿀벌 친화형 고내구성 플라스틱 소초를 제조하였다. 벌 친화적인 플라스틱 소초는 beeswax를 첨가한 polypropylene을 주 소재로 하였으며, PP/beeswax의 낮은 기계적 강도를 보완하기 위하여 무기물 충진재인 활석 (talc) 등을 첨가하여 복합화하고 (Zhang et al., 2016; Graziano et al., 2019), 또한 복합물의 첨가제로서 목분 (woodÁour)이 기계적 물성 강화를 위해 사용되었다 (Sathishkumar et al., 2014; Nikmatin et al., 2017; Lee et al., 2020; Mark et al., 2020).
플라스틱 소초는 다양하게 배합 조성된 PP 복합재료들로부터 사출성형 (injection molding)에 의하여 준개방구조의 형태로 얻어졌다. Field test는 이들 소초 시편들을 가지고 수행되었으며, 소초 성능은 꿀벌의 조소성을 상호 비교함으로써 평가되었다.
실험 방법
1. 재료 및 시험
복합재료로서 기지재인 homo PP와 함께 충진재인 목분 (wood flour), 밀랍 및 활석 (talc) 그리고 상용화제 (compatibilizer)가 사용되었다. 복합재의 기계적 강도 향상을 조사하기 위하여 목분과 활석이 각각 0~7.5 phr 및 0~15 phr가 첨가되었으며, 밀랍의 유무에 따른 물성 변화를 확인하기 위하여 5 phr 및 10 phr 첨가한 복합재가 조성되었다.
복합재료의 주 원료인 polypropylene은 GS Caltex Co.의 H550을 사용하였다. Talc는 KOCHONE Co.의 KC-2000가 그리고 상용화제로는 IruChem Co.의 TPX-1380이 사용되었다. Table 1은 소초용 PP 복합재의 특성 비교를 위하여 시편 번호별로 다양한 배합조성을 보여주고 있다. 여기에서 소초 색상별 조소성을 관찰하기 위하여 염안료를 이용하여 빨강, 노랑 및 검정색을 발현시켰으며, 목분 재료는 침엽수 폐목가루을 사용하여 WPC (50%MB) 형태로 투입되었다.
PP 복합재료의 기계적 물성을 측정하기 위해 Universal Testing Machine (ARG-X STD, Instron)를 사용하여 인장시험 및 3점 굽힘시험을 수행하였다. 인장은 50 mm/min 조건으로 시험하여 인장강도 (tensile strength), 신률 (elongation)을 측정하고, 3점 굽힘 시험은 10 mm/min 조건으로 시험하여 굴곡강도 (Áexual strength) 및 굴곡탄성계수 (Áexual modulus)를 측정하였다. 충격강도는 Izod 충격시험기 (IT 504 Impact Tester, Tinius Olsen)를 사용하여 상온과 저온에서 각각 측정하였다. 물성분석은 인장 ASTM D638, 굴곡 ASTM D790 및 충격 ASTM D256의 기준에 따라 시험되었다.
2. 혼련 및 성형
Compounding (배합) 장치로부터 반죽 (kneading)은 원료의 화학적 변화를 사전 예방할 수 있으면서도 조성물을 균일하게 혼련하기 위하여 PP의 용융온도 (130~171°C)보다 훨씬 높은 250~290°C의 온도 범위에서 약 20 min 동안 수행되었다. 혼련된 배합물은 약 3 mm 두께로 압출 냉각 후, 3 mm 정도의 크기로 절단하여 pellet을 형성시켰다. 성형 단계는 압출 가공된 pellet으로부터 허니콤 구조를 형성하는 과정이며, 이때 소량의 beeswax 조성분은 벌 친화력 증가 외에 성형 점착성을 확보하는 데에도 효과적으로 작용할 수 있다.
현재 보급되고 있는 비정질의 wax 소초는 벌집과 유사한 형태의 roller를 사용하여 calender 성형에 의해 제작되고 있으나, 반결정성 PP 수지의 복합재료 성형은 일반적으로 복잡한 부품을 동일한 품질로 양산할 수 있는 사출 방식을 주로 이용한다. 사출성형에 앞서 시험적으로 open hexagon 형태의 소초가 PLA 필라멘트로부터 3D 프린팅되었다 (Abdelrazeq et al., 2019; Park et al., 2023).
플라스틱 사출용 금형은 소초의 내구성과 조소성을 고려하여 이중 육각형의 뚫린 구조를 갖도록 설계하였으며, Fig. 1에서 그 성형소초의 구조 및 크기가 상세히 표시되고 있다. Fig. 2는 플라스틱 소초 제작을 위하여 사용된 전동식 초고속 사출성형기와 그 내부에 쌍립으로 장착된 두 개의 금형들을 보여준다.
3. Field test
벌집의 재료 조성 및 외관 색상 (노랑, 빨강, 검정 및 자연색)별로 소초를 이용한 벌의 조소 능력이 상호 비교되었다. 또한 양봉장 위치, 양봉 일정 등을 변화시켜 시험을 반복 실시함으로써 변수에 따른 결과의 신뢰성을 제고하였다. 또한 별도로 용융 beeswax를 복합재 소초에 균일하게 spray 코팅하고, 이에 따른 조소성의 변화 정도를 관찰하였다.
현장 적용시험은 전북 완주군에 있는 국립농업과학원 시험양봉장에서 사육 중인 봉군을 대상으로 행하여졌다. 시험에 사용된 봉군은 단상형태로 소비당 4장 소초를 사용하였고 봉군당 약 1만 마리의 벌이 조소를 위해 투입되었다. 벌집판의 성능은 각기 다른 종류의 성형 소초들을 벌통에 함께 넣어두고 벌의 조소력으로 비교 평가하였다.
결과 및 고찰
1. 복합재 특성
벌의 분비물인 밀랍을 소초 제조 조성물에 부가하면, 꿀벌에 대한 친화력을 확보하여 조소 과정에서의 거부감이 없다. 이러한 장점은 소초 제조 후 밀랍을 코팅하는 공정을 별도로 거치지 않더라도 조소성을 향상시킬 수 있을 것이다. 일반적으로 밀랍은 소초의 원료조성에 5~20 wt% 정도 포함될 수 있는 데, 밀랍 성분이 이 범위 이상으로 첨가되는 경우 배합물이 너무 묽어져 제조되는 소초의 치수 안정성을 저해하게 된다. 목분은 목재를 이용한 건축용 자재의 부산물들로서 통상 폐목가루를 건조시킨 후 미분쇄한 것이며, 분쇄 입자는 대개 0.05~1.0 mm 범위의 크기를 가진다. 이러한 목분이 포함된 조성물로 소초를 제조하게 되면, 사용 시에 기계적 강도를 증가시킬 뿐 아니라, 목재에 특징적인 온도조절 기능이 있어 벌 친화적으로 조소율을 높일 수가 있다.
소초용 복합조성물에 밀랍과 목분이 동시에 포함되면, 밀랍의 윤활성이 목분의 분산성을 향상시켜 대면적에서도 상호 균질한 혼합비를 나타냄으로써, 결과적으로 높은 조소율을 갖는 소초가 얻어지게 된다. 일반적으로 밀랍과 목분의 첨가량 합이 10 wt%보다 적으면 소초의 균질한 조성을 기대할 수 없으며, 30 wt%보다 많으면 소초의 내구성을 도모하기 어렵다. 따라서 이들 조성의 중량 합이 10~30 wt%인 범위에서 소초의 치수 안정성이 높고 가공이 용이해진다 (Lee et al., 2022). Table 2는 PP 복합재의 시편 번호별로 각종 기계적 성질을 측정한 결과를 보여준다.
PP 복합재의 밀도는 beeswax를 제외한 각종 첨가제 영향으로 PP 밀도 (0.895~0.920 g/m3)보다 약간 높게 나타났으며, beeswax 첨가는 복합재료의 tensile 및 flexural strength 뿐만 아니라 HDT 특성도 뚜렷이 감소시켰다. 또한 PP 수지에 소량의 상용화제만을 첨가한 복합재 (S7)의 충격강도는 상온 및 저온 시험에서 약 9 J/m의 강도 차이를 보였으나, 다른 각종 유·무기 첨가물을 적절히 부가한 복합재에서는 이러한 차이가 절반 수준으로 감소됨으로써, 저온 충격강도에서 첨가제들이 긍정적인 효과를 나타내었다. 또한 beeswax 성분이 복합재료의 강도 및 경도를 현저히 저하시켰으나 (S11, S12), filler의 첨가는 이러한 beeswax의 영향을 크게 완화할 수 있음을 보여주었다 (S6, S10).
2. 소초 성형
시험용 소초는 벌의 조소 효과가 현장 적용에서 한꺼번에 비교될 수 있도록 시험 조건별로 소초 규격의 1/6~1/3 크기로 절단하여 소광대에 조립하였다. Fig. 3은 3D 프린팅된 각기 다른 색상의 PLA 소초 시편들을 하나의 소초광에 조립한 형태를 보여주고 있다.
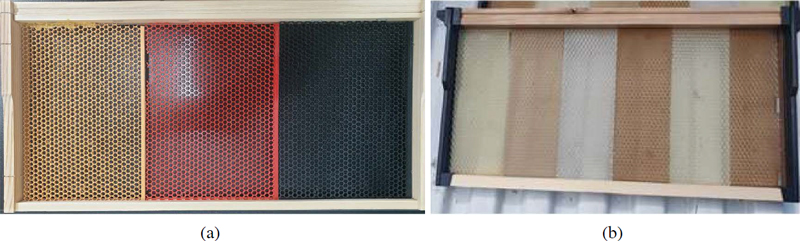
Brood frames assembled with different types of composite combs cut into 1/3 and 1/6 sizes for field testing.
사출성형은 PP 복합재료의 압출 pellet을 사용하여 220 °C의 온도 조건에서 수행되며, 이는 PC 수지의 성형에 적용되는 330°C의 사출온도에 비해 훨씬 낮다. 따라서 외기 열에 의한 얇은 소초 판의 형태 유지가 PC 소재에 비해 다소 취약할 수 있다.
PP 복합재 성형은 색상별 혼합을 방지할 목적으로 색상에 영향이 적은 순서대로 natural, yellow, black 및 red 순으로 사출시켰으며, 재료 조건별로 동일한 재질의 소초들을 얻기 위하여 성형조건 변경 주입 시에 사출된 일정량의 성형품은 시편에서 제외하였다. 벌집 형태 육각형이 서로 교차된 개방형 소초의 구멍은 벌이 집을 지을 때, 필요 물질을 가지고 벌집판의 전후면으로 공기 유통이 가능하도록 얇게 메워진다 (Han, 2012a).
시험용 소초는 벌의 조소 효과가 현장 적용에서 한꺼번에 비교될 수 있도록 시험 조건별로 소초 규격의 1/3 또는 1/6 크기로 절단하여 소광대에 조립되었다. Fig. 3은 현장 적용을 위해 3D 프린팅된 각기 다른 색상의 PLA 소초 시편들과 그리고 사출성형된 여러 가지 PP 소재의 소초 시편들을 하나의 소초광에 조립한 형태들을 보여주고 있다.
3. 벌 조소성
일반적으로 꿀벌은 냄새와 온도에 매우 민감하므로 제조되는 벌집의 친환경성 및 벌의 조소성을 더욱 향상시키기 위하여, 플라스틱 소초에 안전한 밀랍코팅 단계가 부가될 수 있다 (Han, 2012b). 이때 코팅재료는 비싼 beeswax를 대신하여 저렴한 parafÀn wax로 최대 4배까지 혼입할 수 있으나 (Lee et al., 2022), 본 연구에서는 시험 목적상 순수 beeswax 만으로 PP 복합재 소초들에 대한 코팅에 사용하였다. 코팅은 일반적으로 dipping과 spray 방법으로 처리되나, 대개 전자는 120°C이고 후자는 98°C에서 용융된 beeswax를 가지고 행하여지며, 소량 처리에서는 spray가 보다 경제적이어서 많이 활용된다.
Fig. 4는 PLA 소재 기반 소초에 대하여 사양기 유무에 따라 꿀벌의 조소성을 1주에서 8주까지 각 주마다 관찰한 결과이다. 사양기가 있는 벌통 (Fig. 4(a))이 사양기 없는 벌통 (Fig. 4(b))에 비해 초기 조소 능력은 뛰어났으나, 시간이 지남에 따라 사양기 유무에 따른 조소상의 큰 차이는 없었다.
Table 1에서 제시된 배합조성의 시편번호 S1~S6으로부터 소초 색상 (노랑, 빨강, 검정 및 자연색)에 주안점을 두고 현장 적용시험을 실시하였다. Fig. 5는 외관 색상별로 벌 조소성을 비교하기 위하여 벌통 내 해당 소초광의 위치를 다르게 배열시켜 2주 동안 시험한 결과이다. 여기서 소초광 위치에 따른 숫자는 시편번호를 가리킨다. 시험 소초들이 벌통 배치 후 3, 7, 9 및 13일 경과에 이르기까지 유의미한 조소 차이를 보이지 않음으로써, 사실상 벌 조소력이 소초의 외관 색상에 별 영향을 받지 않는 것 같다.
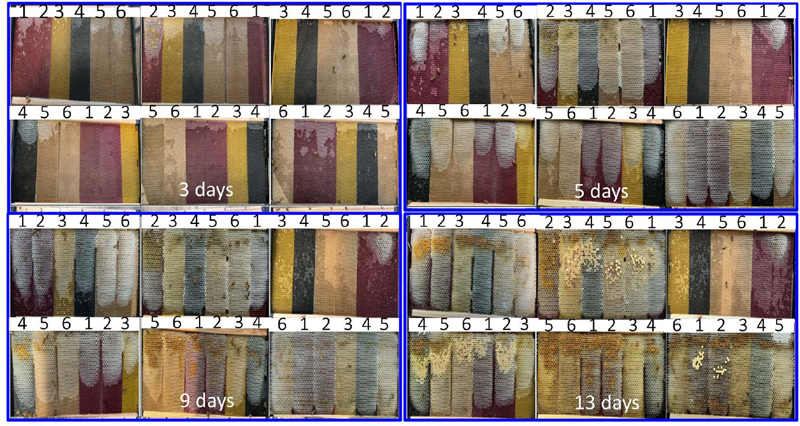
A test evaluation on bees’ nesting ability of plastic comb foundations by color. The upper numbers refer to the specimen numbers in Table 1.
Table 1의 시편번호 S7~S12에 대하여 소초 재질에 주안점을 두고 현장 적용시험을 실시하였다. Fig. 6은 첨가물 조성별로 벌 조소성을 비교하기 위하여 벌통 내 해당 소초광의 위치를 다르게 배열시켜 2주 동안 관찰한 결과이다. 여기서 Fig. 6(a)의 소초는 표면에 어떠한 별도의 처리가 없었으나, Fig. 6(b)의 소초 외부는 beeswax로 충분히 코팅되었다.
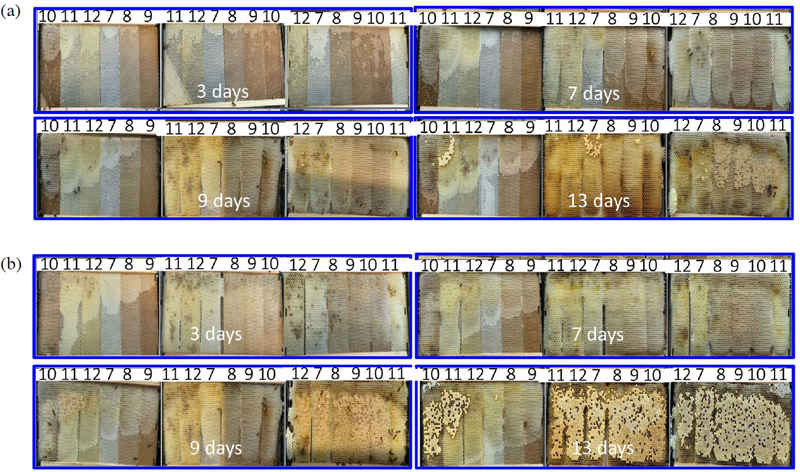
Evaluation of nesting ability of comb foundation materials (a) without any coating and (b) with beeswax coating. The upper numbers refer to the specimen numbers in Table 1.
이 벌통 배치 후 3, 7, 9 및 13일의 경과에서 시편번호 10, 11 및 12의 소초들은 beeswax 첨가 조성들을 가지고 뚜렷한 조소 효과를 보였으나, beeswax 함량 5, 10 및 15 phr에 따른 조소력 차이는 그리 크지 않았다. 따라서 소초에 beeswax 함량이 많을수록 그 강도는 더 낮아지므로, 소초의 beeswax 배합조성은 가능한 최소 함량인 5 phr이 바람직하다.
또한 beeswax 첨가 조성의 소초들에서 beeswax 코팅 유무에 따라 조소력은 7일 경과 시 70% 그리고 13일 경과 시 80% 수준으로 점차 그 차이가 좁혀지고 있다. 이것은 시간이 지남에 따라 외부의 beeswax는 열화되고 있는 반면, 내부의 beeswax 성분은 서서히 표면으로 용출하는 데에 기인한다. 따라서 장기적 사용 관점에서 beeswax 내부조성을 가진 소초는 조소력 향상을 위해 별도의 코팅처리를 반드시 행할 필요는 없을 것으로 생각한다.
적 요
플라스틱 소초는 다양하게 배합조성된 PP 복합재료들로부터 사출성형 (injection molding)에 의해 개방구조의 형태로 얻어졌다. 이들 복합재료는 기지재인 homo Polypropylene와 함께 충진재로서 목분, 밀랍 및 활석 그리고 상용화제 (compatibilizer)가 사용되었다. 첨가된 beeswax 성분은 복합재의 기계적 강도를 현저히 떨어뜨렸지만, Àller 함량의 증가를 가지고 소초의 기계적 성질에 미치는 beeswax 영향을 크게 완화시킬 수 있음을 확인하였다. 이들 소초 시험편들의 성능은 Àeld test에서 꿀벌의 조소력을 상호 비교함으로써 평가되었다. 소초의 외관 색상 및 beeswax 조성에 대하여 관찰한 결과, 색상이 벌의 조소에 끼치는 영향은 그리 뚜렷하지 않은 반면, beeswax 첨가는 비록 함량별 (5~15 phr) 조소력의 차이는 크지 않았으나 조소성 향상에 뚜렷이 기여하였다. 따라서 beeswax의 최소 배합조성을 가진 S11이 효과적인 선택이며, beeswax 성분 첨가에 따른 소초재의 기계적 성질 저하 방지를 위하여 추가적인 Àller의 함량 증가가 필요하다.
Acknowledgments
본 연구는 농촌진흥청 농업정책지원기술개발사업의 지원으로 수행되었습니다 (과제번호 RS-2021-RD010194).
References
-
Abdelrazeq, H., P. Sobolčiak, M. A. A. Al-Maadeed, M. Ouederni and I. Krupa. 2019. Recycled Polyethylene/Paraffin Wax/Expanded Graphite Based Heat Absorbers for Thermal Energy Storage: An Artificial Aging Study. Molecules 24(7): 1217.
[https://doi.org/10.3390/molecules24071217]
-
Graziano, A., S. Jaffer and M. Sain. 2019. Review on modification strategies of polyethylene/polypropylene immiscible thermoplastic polymer blends for enhancing their mechanical behavior. J. Elastomers Plast. 51(4): 291-336.
[https://doi.org/10.1177/0095244318783806]
- Han, D. H. 2012a. Development of Beehive with Plastic Foundation. Proceedings of the KAIS Fall Conference 2012.05b: 789-792.
- Han, D. H. 2012b. A Study on the Safety of Bees Wax. Proceedings of the KAIS Fall Conference 2012.05b: 793-795.
- Hwang, T. S. 2021. A compound composite for honeycomb and honeycomb manufacturing method thereof. Korea open patent 10-2021-0108095.
-
Lee, C., M. M. Pang and S. C. Koay. 2020. Talc filled polylactic-acid biobased polymer composites: tensile, thermal and morphological properties. SN Appl. Sci. 2: 354.
[https://doi.org/10.1007/s42452-020-2172-y]
-
Lee, S. G., A. Lim, T. S. Hwang, D. Kim, S. B. Kim, M. Y. Lee and J. H. Kim. 2022. Polypropylene Compounding Compositions for Fabrication of Plastic Honeycomb Foundation. J. Apic. 37(2): 143-149.
[https://doi.org/10.17519/apiculture.2022.06.37.2.143]
-
Mark, U. C., I. C. Madufor, H. C. Obasi and U. Mark. 2020. Influence of filler loading on the mechanical and morphological properties of carbonized coconut shell particles reinforced polypropylene composites. J. Compos. Mater. 54(3): 397-407.
[https://doi.org/10.1177/0021998319856070]
-
Nikmatin, S., A. Syafiuddin, A. Kueh and A. Maddu. 2017. Physical, thermal, and mechanical properties of polypropylene composites filled with rattan nanoparticles. J. Appl. 15(4): 386-395.
[https://doi.org/10.1016/j.jart.2017.03.008]
-
Park, J., J. H. Kim, Y. S. Cho, Y. Y. Jo and S. G. Lee. 2023. FDM-typed Additive Manufacturing and Optimization of Polypropylene/Beeswax Composites for Beehive Application. J. Apic. 38(3): 297-306.
[https://doi.org/10.17519/apiculture.2023.09.38.3.297]
-
Sathishkumar, T. P., S. Satheeshkumar and J. Naveen. 2014. Glass fiber-reinforced polymer composites - a review. J. Reinf. Plast. Compos. 33(13): 1258-1275.
[https://doi.org/10.1177/0731684414530790]
-
Semkiw, P. and P. Skubida. 2013. Comb construction and brood development on beeswax foundation adulterated with paraffin. J. Apic. Sci. 57(1): 75-83.
[https://doi.org/10.2478/jas-2013-0009]
-
Svečnjak, L., O. Jović, S. Prđun, J. Rogina, Z. Marijanović, J. Car, M. Matošević and I. Jerković. 2019. Influence of beeswax adulteration with paraffin on the composition and quality of honey determined by physicochemical analyses, 1H NMR, FTIR-ATR, and HS-SPME/GC-MS. Food Chem. 291: 187-198.
[https://doi.org/10.1016/j.foodchem.2019.03.151]
-
Zhang, L. J., W. Xu and Y. Fu. 2016. Effect of SiO2/EVA on the mechanical properties, permeability, and residual solvent of polypropylene packaging films. Polym. Compos. 37(1): 101-107.
[https://doi.org/10.1002/pc.23159]
-
Zhang, Z., S. Liu and Z. Tang. 2011. Comparisons of honeycomb sandwich and foam-filled cylindrical columns under axial crushing loads. Thin-Walled Struct. 49(9): 1071-1079.
[https://doi.org/10.1016/j.tws.2011.03.017]